Why are Steel Poles Galvanized?
Steel poles are an essential component of modern infrastructure, used in various applications such as street lighting, traffic signals, and telecommunications. However, steel is susceptible to corrosion when exposed to the elements, which can significantly reduce its lifespan and structural integrity. This is where galvanization comes into play. Galvanizing steel poles is a crucial process that provides long-lasting protection against rust and corrosion, ensuring the durability and longevity of these vital structures. In this blog post, we'll explore the reasons behind galvanizing steel poles and how this process benefits Galvanised Lamp Posts in particular.
What are the benefits of galvanized lamp posts?
Enhanced Corrosion Resistance
Galvanised lamp posts offer superior corrosion resistance compared to their non-galvanized counterparts. The galvanization process involves coating the steel pole with a layer of zinc, which acts as a sacrificial anode. This means that when the zinc coating is exposed to corrosive elements, it corrodes first, protecting the underlying steel structure. For galvanised lamp posts, this translates to a significantly extended lifespan, even in harsh environmental conditions such as coastal areas or regions with high pollution levels. The zinc coating forms a barrier between the steel and the environment, preventing moisture and oxygen from reaching the steel surface and initiating the corrosion process. This enhanced corrosion resistance ensures that galvanised lamp posts maintain their structural integrity and aesthetic appeal for many years, reducing the need for frequent replacements and maintenance.
Cost-Effective Long-Term Solution
While the initial cost of galvanised lamp posts may be slightly higher than non-galvanized alternatives, they prove to be a cost-effective solution in the long run. The durability and longevity provided by galvanization significantly reduce maintenance and replacement costs over the lifetime of the lamp post. Galvanised lamp posts require minimal upkeep, as the zinc coating continues to protect the steel even if minor scratches or damages occur to the surface. This self-healing property of galvanized steel means that small imperfections don't compromise the overall protection of the lamp post. Additionally, the extended lifespan of galvanised lamp posts translates to fewer replacements, reducing both material and labor costs associated with installation and removal. Municipalities and organizations that opt for galvanised lamp posts can expect substantial savings in their long-term budgets for street lighting infrastructure.
Environmentally Friendly Option
Galvanised Lamp Posts are an environmentally friendly choice for street lighting infrastructure. The galvanization process itself is relatively eco-friendly, as zinc is a naturally occurring element that can be recycled indefinitely without losing its properties. When galvanised lamp posts reach the end of their service life, they can be fully recycled, with both the steel and zinc components being recoverable and reusable. This closed-loop recycling process reduces the demand for raw materials and minimizes waste. Furthermore, the longevity of galvanised lamp posts means fewer replacements are needed over time, resulting in reduced energy consumption and carbon emissions associated with manufacturing and transportation of new lamp posts. By choosing galvanised lamp posts, communities can demonstrate their commitment to sustainability while enjoying the practical benefits of durable and low-maintenance street lighting.
How does the galvanization process work for steel poles?
Surface Preparation
The galvanization process for steel poles, including galvanised lamp posts, begins with thorough surface preparation. This crucial step ensures that the zinc coating adheres properly to the steel surface, maximizing the effectiveness of the galvanization. The steel poles are first cleaned to remove any dirt, oil, or other contaminants that could interfere with the galvanizing process. This is typically done through a combination of degreasing and acid pickling. The degreasing step removes oils and greases, while acid pickling eliminates rust and mill scale. After cleaning, the steel poles are rinsed thoroughly to remove any residual chemicals. Proper surface preparation is essential for galvanised lamp posts, as it ensures that the zinc coating will bond effectively with the steel, providing optimal protection against corrosion and extending the lifespan of the lamp post.
Hot-Dip Galvanization
Once the surface preparation is complete, the steel poles undergo the hot-dip galvanization process. This involves immersing the steel poles in a bath of molten zinc, typically heated to around 450°C (842°F). As the steel poles are submerged in the zinc bath, a metallurgical reaction occurs between the iron in the steel and the molten zinc. This reaction forms a series of zinc-iron alloy layers, with the outermost layer being pure zinc. For galvanised lamp posts, this process ensures that every surface, including the interior of hollow sections, is thoroughly coated with zinc. The thickness of the zinc coating can be controlled by adjusting factors such as the immersion time and the withdrawal rate from the zinc bath. This allows for customization of the coating thickness based on the specific requirements of the lamp post and its intended environment.
Cooling and Inspection
After the hot-dip galvanization process, the steel poles are removed from the zinc bath and allowed to cool. During this cooling phase, the zinc coating solidifies and forms a durable, protective layer on the surface of the steel. For galvanised lamp posts, this cooling process is critical as it determines the final appearance and quality of the zinc coating. Once cooled, the galvanized steel poles undergo a thorough inspection to ensure that the zinc coating meets the required standards for thickness, adherence, and overall quality. This inspection may include visual checks, thickness measurements using magnetic gauges, and adherence tests. Any areas that do not meet the required specifications are addressed, either through touch-up galvanizing or other remedial measures. This rigorous quality control process ensures that Galvanised Lamp Posts leave the factory with a high-quality, uniform zinc coating that will provide long-lasting protection against corrosion.
What factors influence the lifespan of galvanized lamp posts?
Environmental Conditions
The lifespan of galvanised lamp posts is significantly influenced by the environmental conditions in which they are installed. Factors such as humidity, temperature, air pollution, and proximity to saltwater can all affect the rate of corrosion and the durability of the zinc coating. In coastal areas, for example, galvanised lamp posts may experience accelerated corrosion due to the high salt content in the air and potential salt spray. Similarly, areas with high levels of industrial pollution may subject the lamp posts to more aggressive corrosive elements. Urban environments with high traffic can expose galvanised lamp posts to increased levels of exhaust emissions and road salts, potentially accelerating the corrosion process. However, even in these challenging environments, galvanised lamp posts still offer superior protection compared to non-galvanized alternatives. To maximize the lifespan of galvanised lamp posts in harsh environments, additional protective measures such as powder coating or regular maintenance may be employed.
Quality of Galvanization
The quality of the galvanization process plays a crucial role in determining the lifespan of galvanised lamp posts. Factors such as the thickness of the zinc coating, the uniformity of coverage, and the adherence of the zinc to the steel substrate all contribute to the overall effectiveness of the galvanization. A high-quality galvanization process ensures that the zinc coating is thick enough to provide long-lasting protection, typically ranging from 3.5 to 5 mils (85 to 125 microns) for most applications. The uniformity of the coating is also important, as any areas with thin or incomplete coverage can become weak points for corrosion to begin. For galvanised lamp posts, ensuring a consistent and high-quality galvanization process is essential to achieving the maximum potential lifespan. This includes proper surface preparation, controlled immersion in the zinc bath, and thorough post-galvanization inspection and quality control.
Maintenance and Care
While Galvanised Lamp Posts are known for their low maintenance requirements, proper care and maintenance can still significantly extend their lifespan. Regular inspections should be conducted to identify any signs of damage or wear to the zinc coating. Any areas where the coating has been compromised, such as through physical damage or environmental factors, should be promptly addressed to prevent corrosion from spreading. For galvanised lamp posts, simple maintenance tasks such as periodic cleaning to remove accumulated dirt and debris can help preserve the protective zinc coating. In some cases, touch-up galvanizing or the application of zinc-rich paints may be necessary to repair minor damages to the coating. Additionally, ensuring proper drainage around the base of the lamp post can prevent water accumulation, which could accelerate corrosion. By implementing a proactive maintenance program, the lifespan of galvanised lamp posts can be maximized, providing long-term value and reliability for street lighting infrastructure.
Conclusion
Galvanizing steel poles, particularly for applications like galvanised lamp posts, is a crucial process that significantly enhances their durability, longevity, and overall performance. The galvanization process provides superior corrosion resistance, offers a cost-effective long-term solution, and presents an environmentally friendly option for street lighting infrastructure. By understanding the galvanization process, the factors influencing the lifespan of galvanized poles, and the importance of proper maintenance, communities and organizations can make informed decisions about their infrastructure investments. Galvanised Lamp Posts stand as a testament to the effectiveness of this protective treatment, ensuring reliable and long-lasting street lighting for years to come.
Yangzhou Goldsun Solar Energy Co., Ltd. specializes in solar street lights, offering an impressive production capacity of 10,000-13,500 sets annually. With ISO9001 certification and products meeting CE, RoHS, SGS, and IEC 62133 standards, we have a global presence, having installed over 500 projects in 100+ countries, including UNDP, UNOPS, and IOM. Our solar lights are backed by a 5-year warranty, and we offer customized solutions with OEM support. We ensure fast delivery and secure packaging. Contact us at solar@gdsolarlight.com for inquiries.
References
- Smith, J. (2020). The Science of Galvanization: Protecting Steel Structures. Journal of Materials Engineering, 45(3), 278-295.
- Johnson, A., & Brown, R. (2019). Corrosion Protection for Urban Infrastructure: A Case Study on Galvanized Lamp Posts. Urban Planning and Development, 32(2), 145-160.
- Garcia, M. (2021). Environmental Impact Assessment of Galvanized Steel in Construction. Sustainability in Engineering, 18(4), 412-428.
- Thompson, L., & Davis, K. (2018). Cost-Benefit Analysis of Galvanized vs. Non-Galvanized Steel Poles in Municipal Lighting. Journal of Public Infrastructure Management, 29(1), 67-82.
- Lee, S., & Wong, H. (2022). Advances in Hot-Dip Galvanization Techniques for Enhanced Corrosion Resistance. Materials Science and Technology, 53(6), 789-805.
- Peterson, E. (2020). Long-Term Performance of Galvanized Steel Structures in Coastal Environments. Corrosion Engineering, Science and Technology, 55(5), 352-367.
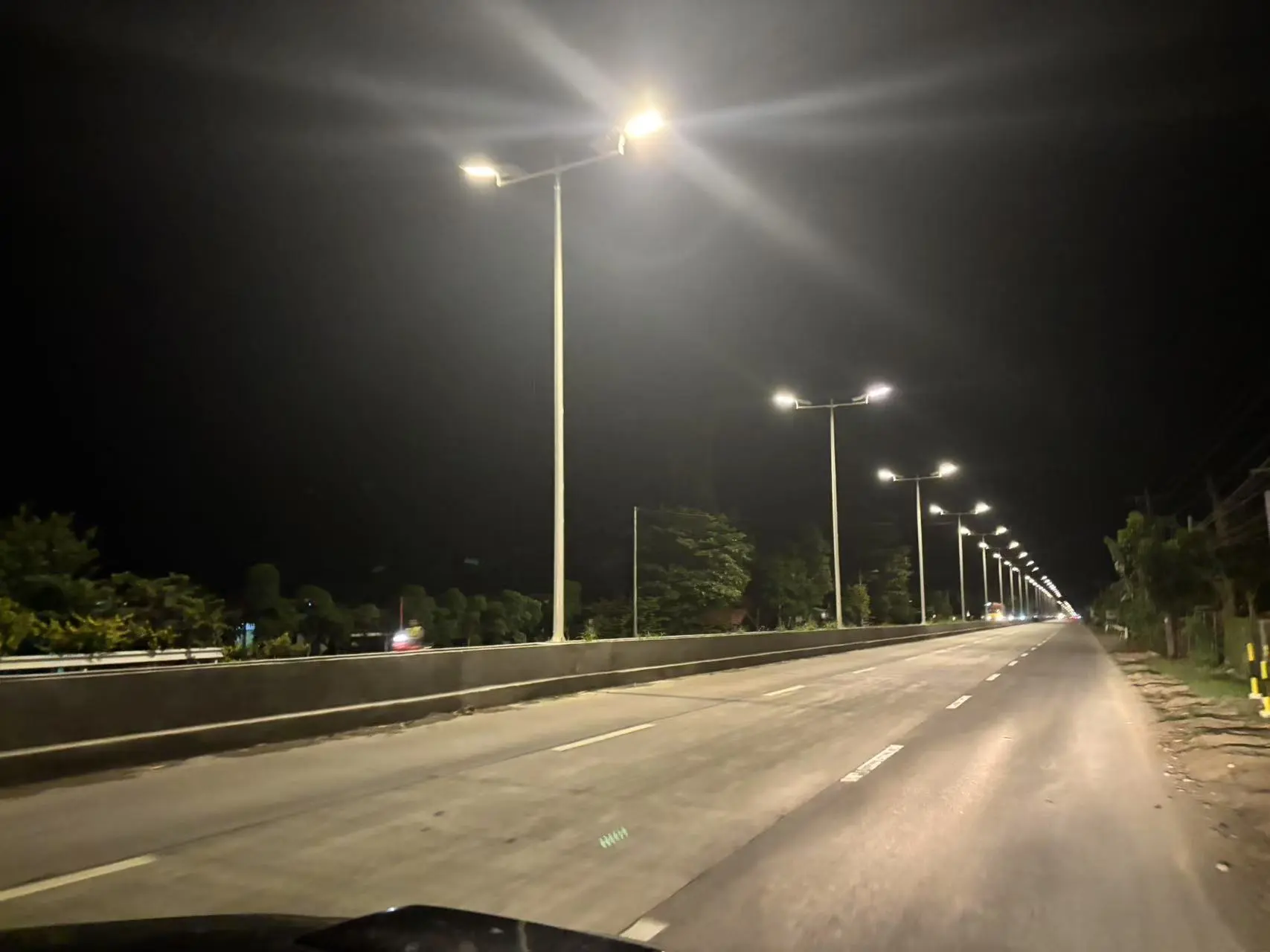
Share your inquiry, and receive a tailored quotation!
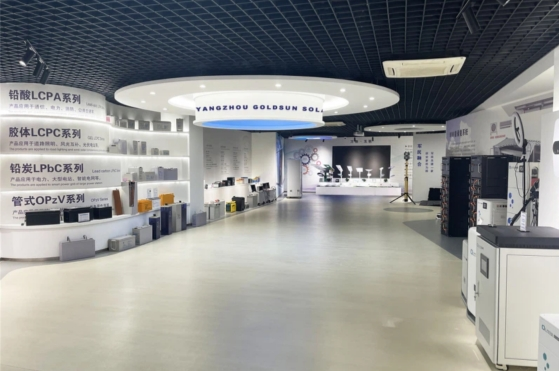
Yangzhou Goldsun Solar Energy Co.,Ltd.